
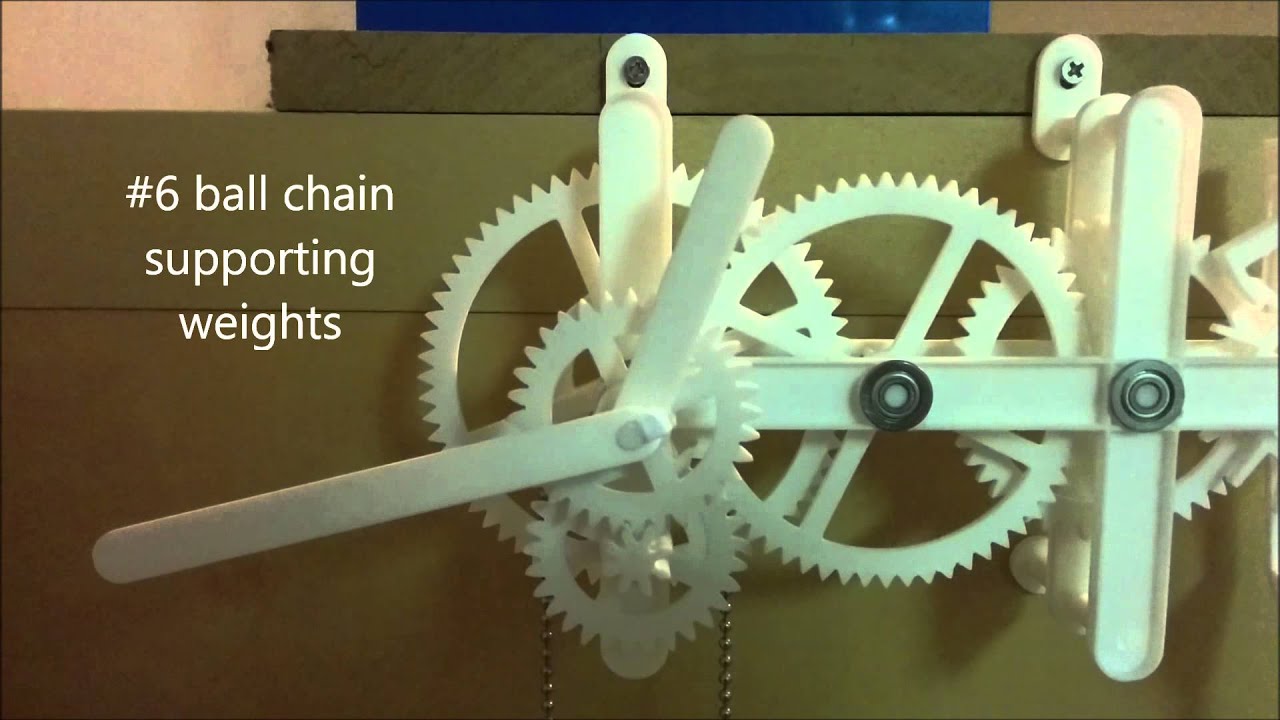
- #3d printed mechanical clock upgrade#
- #3d printed mechanical clock pro#
- #3d printed mechanical clock software#
The case is the body of your mechanical keyboard, and it holds the switches and other electronic components. If you really want to take the plunge and get your own 3D printer, we’ve put together a guide with everything you need to know before you buy one.ġ. Making your own parts, on the other hand, can reduce that cost to less than $50.Īnd don’t get deterred if you don’t have a 3D printer at home-you can always sign up for a membership at your local maker space where there will likely be machines you can use and even classes you can attend. Ordering your components will generally be more expensive, resulting in a final price tag of around $150. A high-end peripheral can easily cost in excess of $100, so we designed this project to be generally affordable, and if you want to cut costs further, you can even 3D-print your case. If you’re ready for an adventure, here’s how you can build your own 65-percent mechanical keyboard. But there’s only one way that gives you the satisfaction of having made a keyboard that’s specifically made for you and by you. Choosing one approach or the other may not make a huge difference in the price tag of your new peripheral.
#3d printed mechanical clock upgrade#
If you want to upgrade your typing experience with one of these gadgets, there are two ways to go about it: You can always buy one or, if you’re up for the challenge, put one together yourself. Mechanical keyboards are all the rage and it’s easy to see why-there’s the pleasure of being able to really hit the keys, the clicky sounds, and the fact that they can be highly customizable. (You can also view a video of the making of the clock below.We may earn revenue from the products available on this page and participate in affiliate programs. The clock’s appearance is as original as all of the ways he chose to create this exceptional object. In general, Olczyk’s clock shows how several different machines are not only captured in one, but that using a hybrid 3D printer can yield some stunning results.
#3d printed mechanical clock software#
(He also used Voxelizer software with the ZMorph.) The materials he used include: Fiber Force Silver Glitter High Speed PLA, Acrylic glass (4 mm), Plexiglas (2 mm), and adhesive foil.
#3d printed mechanical clock pro#
To make the clock, Olczyk used the ZMorph Essential Set with one Plastic Extruder 1.75 mm Toolhead, one CNC PRO milling Toolhead, and one Laser Toolhead.
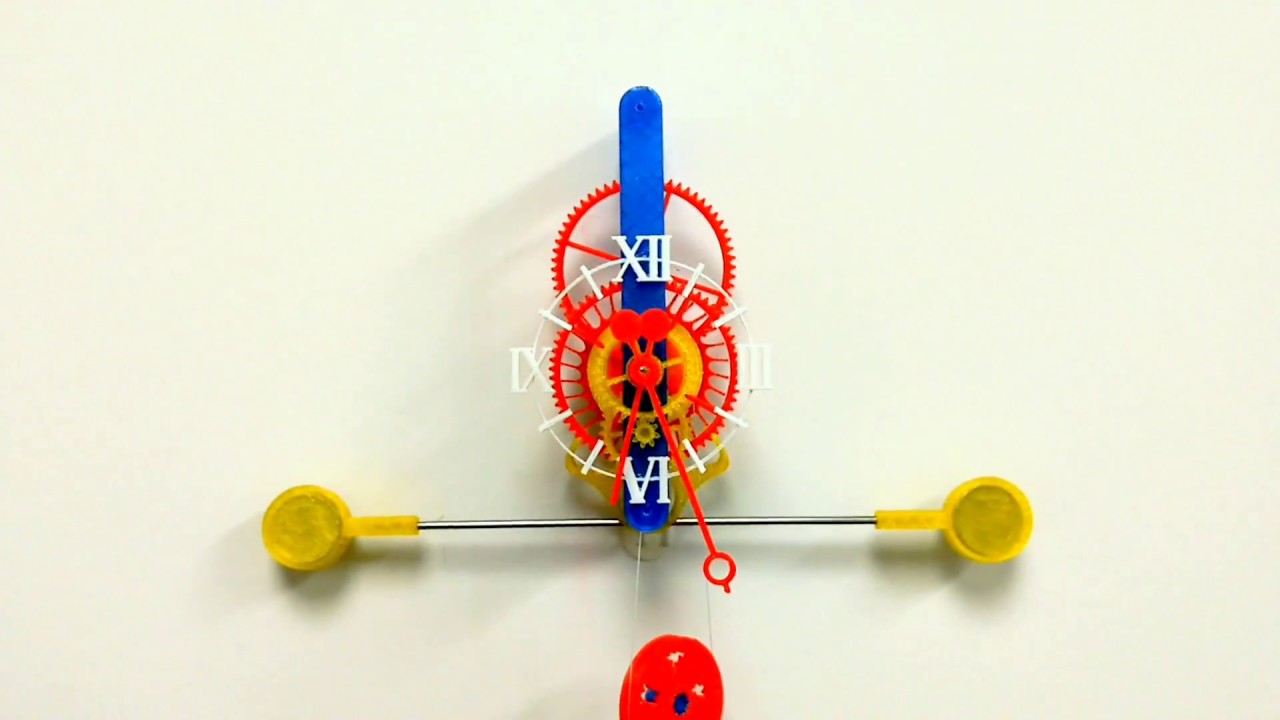
CNC milling and laser cutting were able to step in where 3D printing didn’t work for Olczyk, and the ability to simply switch out toolheads made all of the difference for the overall appearance and functioning of his clock. Here, 3D printing was not capable of realizing Olczyk’s design on its own, mainly because 3D printing offered only limited materials for making the clock. In its completed form you can see how the clock, which is quite elaborately designed, benefits from the use of all three of the ZMorph’s different toolheads. You have to admit: the results are quite impressive! Finally, the laser cutter toolhead cut the clock’s numbers from black adhesive foil, instead of having to manually cut and place each number on the face of the clock. These milled parts are made of translucent Plexiglas, which makes the clock look more refined, as it also retains its lightweight appearance. Olczyk chose to use the CNC milling toolhead to make sturdy gears. For example, 3D printing works best to make small and medium sized objects with complex structures, it works well where there’s mechanical wearing, and it allows the parts to be fabricated in one piece. Olczyk’s clock looks a bit like an antique, although it is made with the latest cutting edge technologies. And from viewing this project we also learn the strengths and weaknesses of the different kinds of machines available to designers today. Olczyk’s clock was assembled using about 80 different parts, almost all of which consist of gears, that were made using the ZMorph 2.0 S Hybrid 3D Printer. Olczyk’s choice to use the ZMorph, which combines CNC milling, laser cutting, and 3D printing, demonstrates some of a hybrid 3D printer’s advantages for projects requiring more than just 3D printing technology. This system allows one printer to perform multiple functions with just a simple switch of the toolheads, saving space and cost along the way.

What makes his Custom Mechanical Clock so unique is that it was made with a ZMorph Hybrid 3D printer that has an interchangeable toolhead system.

But Olczyk wanted to do something different. Usually when a project uses different materials and is produced by different technologies it requires separate machines for the 3D printing, laser cutting, and CNC milling aspects of the project. But his trick was that he was able to use the same machine to do it, simply switching by switching out toolheads. Matt Olczyk has designed, printed, milled and cut a pretty incredible looking Custom Mechanical Clock.
